Inspiration
Trak Packer: Our First Six-Week Sprint
Follow the Loupe team as we take the New Machine Concept for our revolutionary Trak Packer and turn it into a shippable product.
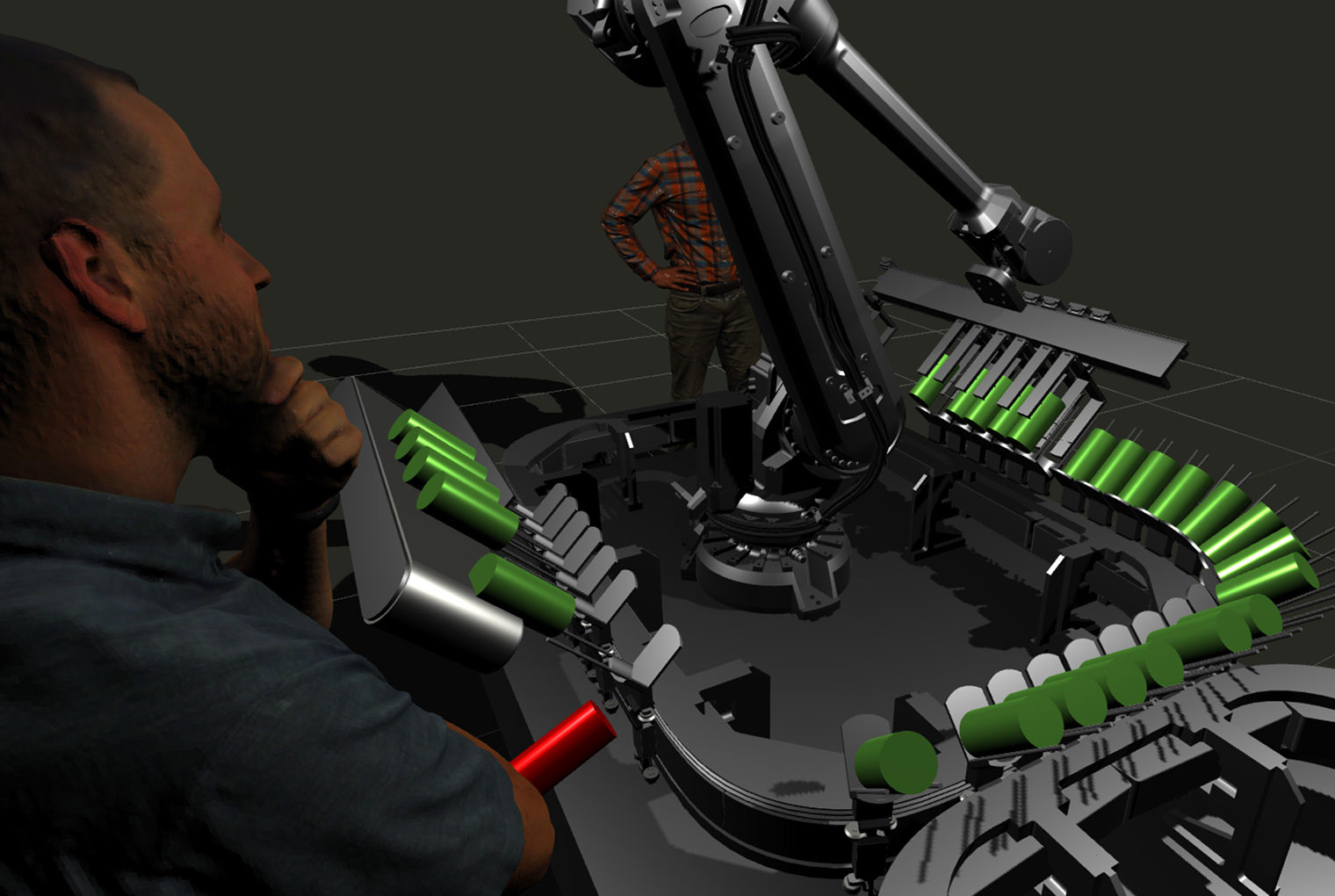
It’s a wrap! Loupe just completed our second season of Live at Loupe — our YouTube livestream series featuring the real-time development of our machines. In season one, we explored a revolutionary idea introduced by B&R’s ACOPOStrak technology: What if there was a machine that could transition between different product configurations without any changes in hard tooling?
We dubbed this the Trak Packer — an exciting machine capability that would enable the case packing of a wide variety of product inputs, without losing 30–60 minutes for every changeover to a new product or case type.
Season one was devoted to creating a New Machine Concept — Loupe’s proprietary process for translating back-of-the-napkin ideas into workable blueprints. Our team produced a complete proposal for what it would take to build the Trak Packer, including iterative CAD designs, timing studies, and controls architecture.
Making it Real
While season one’s CAD design did a good job of conveying the possibilities, a 3D model is far from a finished product. Eventually, we’ll need to cut metal parts and program interactive controls for this machine — which means for this season, it’s time to dial in specifics.
In other words, we have our work cut out for us. In this season, we move into our development process — and in particular, our unique Ship in Six methodology. Our charge is to figure out how to produce a shippable, finished version of the Trak Packer in a six-week sprint.
One thing that makes this season unique is that in respect to social distancing guidelines, the entire Loupe team is currently working remotely — which means all of our collaborative sessions happen virtually.
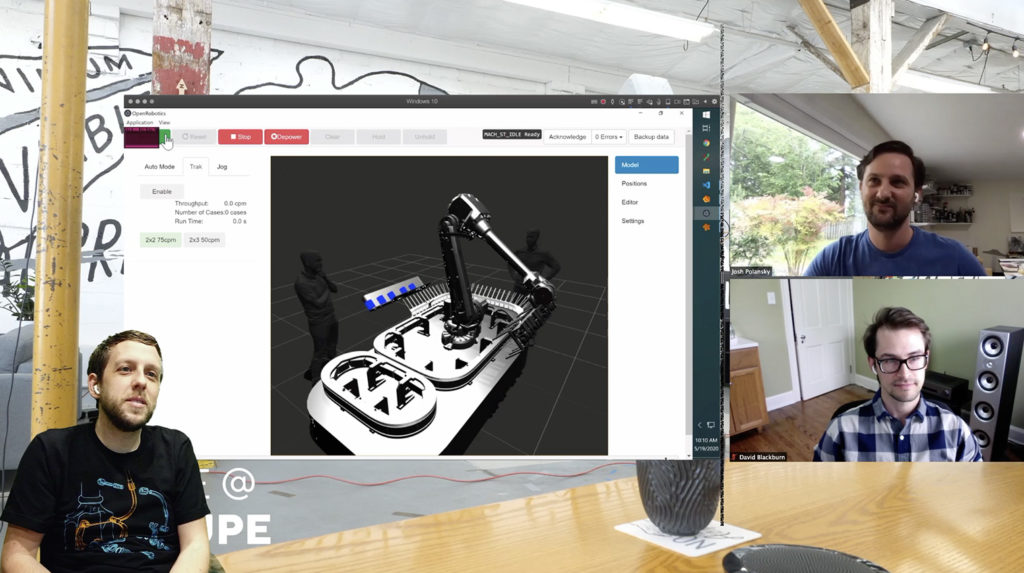
Fortunately, Loupe has long been a pioneer of new working strategies and environments and is well-equipped to weather this shift. Even while sharing complex simulations over Zoom, we face no demo glitches and are able to collaborate seamlessly.
Scope
Our first step is to determine the scope for this sprint: What could we reasonably expect to ship in the next six weeks? You can experience this initial discussion in Episode 1.
We decide on a digital twin of the ABB robot, track, and shuttles. This will be similar to the 3D model, but more robust — built in a software platform that precisely mimics the conditions of running the actual machine, with every bolt and code phrase accounted for. This digital twin allows us to program the behaviors of the robot, the command interface, the timing of the machine, as well as the product infeed and output conveyors for boxes of product.
Discovery
At Loupe, one of our core values is to “Think Critically” — which means that to make this machine shippable, we need to ask hard questions, challenge assumptions, and not take anything for granted. As we explore the use case and feasibility of our idea, we run into a number of interesting conundrums.
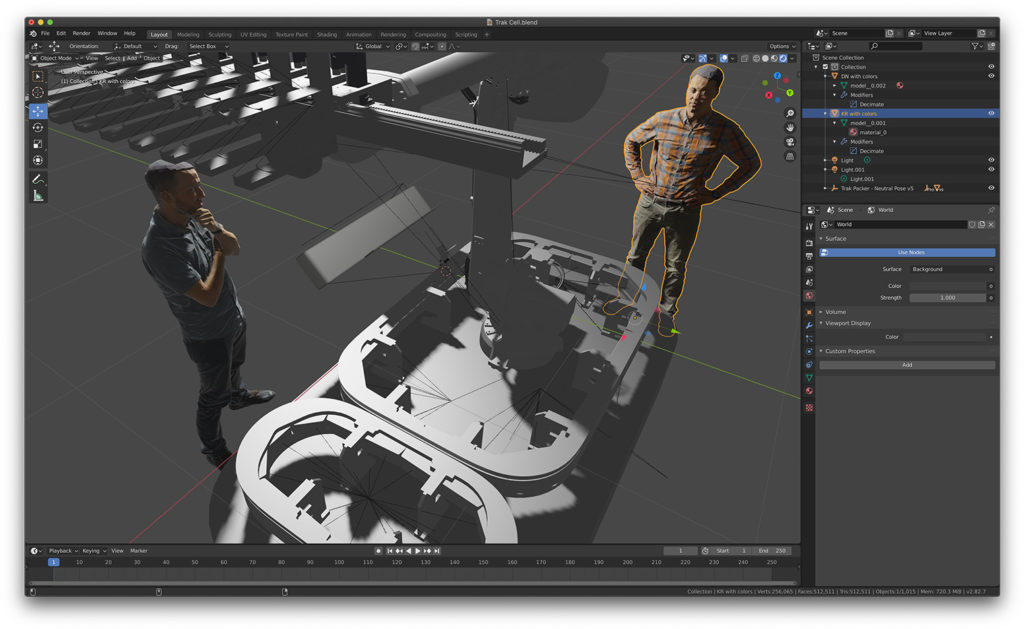
For example, one of the first questions we need to answer is whether to use Robotware and RobotStudio to control the robot, or to use Automation Runtime (B&R’s real-time operating system) to do both the machine control and the robot control in one controller. You can hear more about this as well as additional questions we explore on Episode 2.
While RobotStudio offers additional power, we have to consider both the target audience and the deliverable of the project. We’ll likely be interacting with business leaders, not development teams — and we want the ability to deliver the Trak Packer to a customer in a way that they can interact with it virtually. RobotStudio would require that they download an instance of the software to get the functionality of a virtual controller. So for this sprint, we elect to build the digital twin with all B&R components.
In Episode 3, we also review the infrastructure of both the user interface data and Automation Studio — and in particular, the strength of a Machine-Centric approach.
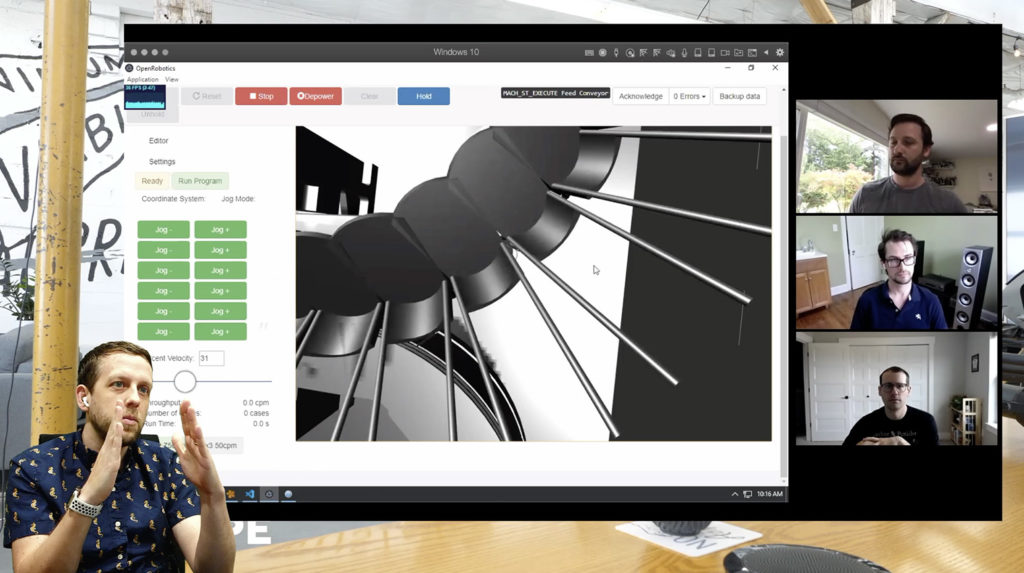
Refinement
Producing this digital twin means managing a number of (literal) moving parts — including the robot, shuttles, and the product itself. Coordinating the precise movements and timing of each component requires complex choreography.
The power of our collaborative, iterative process is that it enables us to be agile and respond to new information as it reveals itself. Not surprisingly, in this stage we run into challenges we could not have anticipated until having a working model.
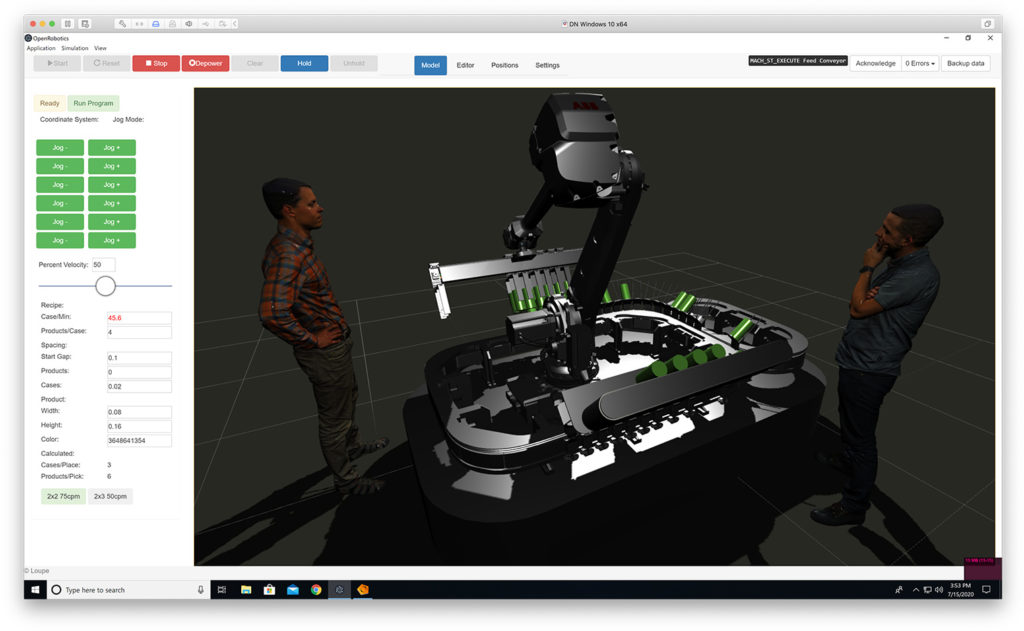
Our work in Episode 4 discusses how the machine will handle error recovery, when a shuttle needs to stop for some reason. Episode 5 brings us new challenges with the product infeed and the alignment of shuttles to the conveyor — since they are aligned in velocity but not space.
In Episode 6, we feel the looming presence of our 6-week timeline, where it becomes easier to prioritize any final issues in order to produce a shippable demo.
Deliverable
In the end, we are able to create a comprehensive digital model that allows us to address all limitations and challenges before building an actual machine. And in doing so, we greatly expand our audience of potential customers by making the idea more accessible.
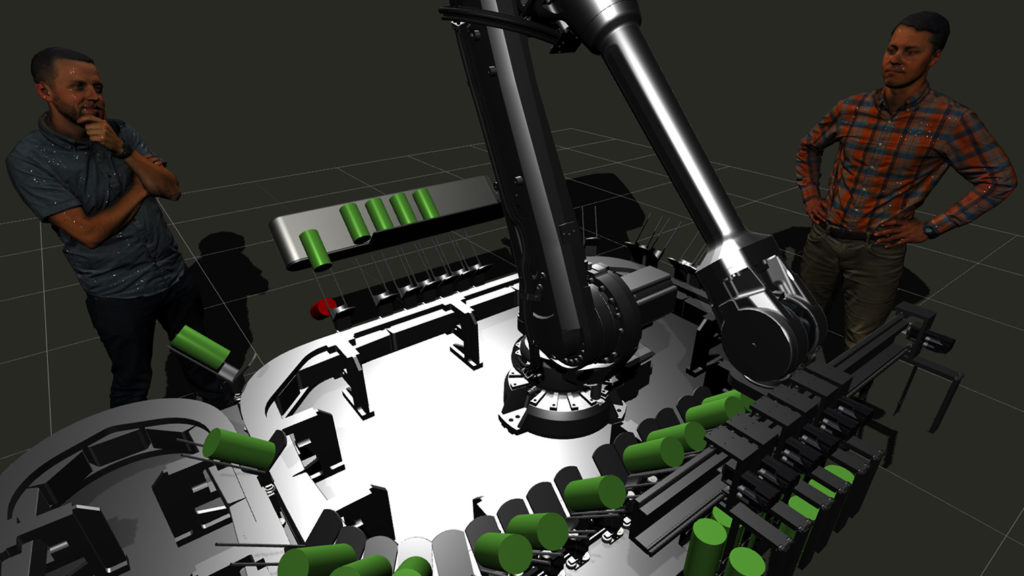
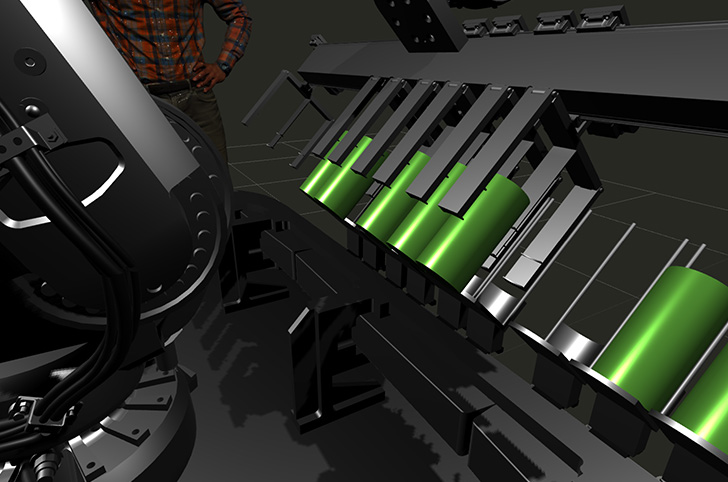
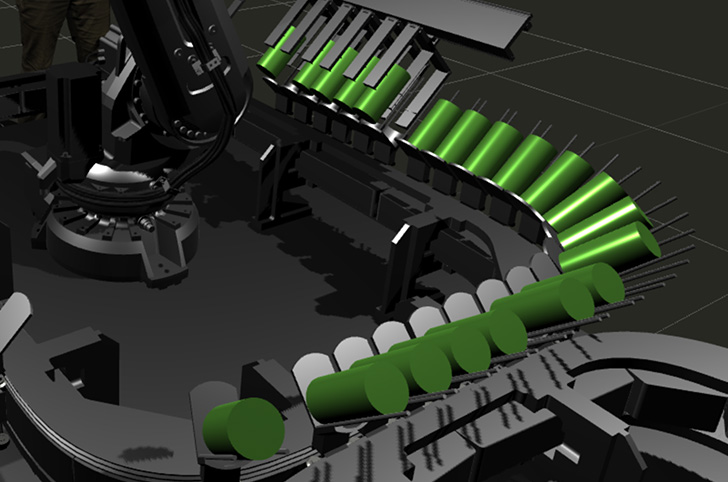
Or, to quote our CEO and Co-Founder David Nichols:
“We took the audience of people who could understand this machine, and increased it by a factor of 10. Before this, we could tell people about it for two hours and they might get it. When we did the New Machine Concept, more people had the opportunity to get it. But now that we have this digital twin, a lot more people will get it instantly. Now we can show it to more people, get more funding, create momentum, and get people excited about it. That’s why we do a 6-week sprint: without this demo, people wouldn’t understand what we were talking about.”
Thanks again for joining us for season two of Live at Loupe! Stay tuned for more next season, as we explore the real-time development of more revolutionary machine concepts and technologies.