Inspiration
Trak Packer: A New Machine Concept
Our revolutionary YouTube livestream series just completed its first season — following our team as we create a New Machine Concept for the Trak Packer.
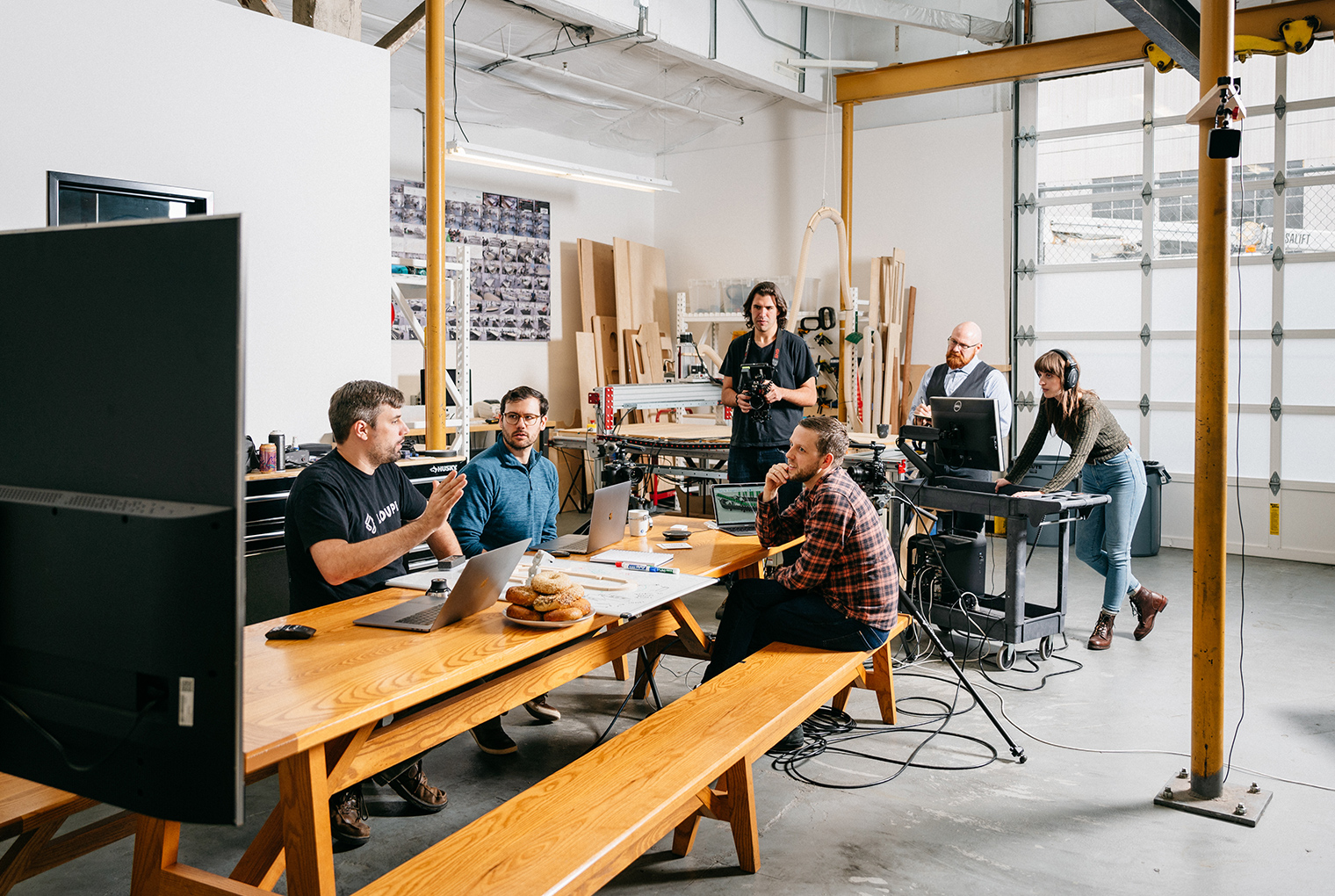
We are excited to announce the completion of our first season of Live at Loupe! For those of you who haven’t been following along, we recently launched a YouTube livestream series featuring the real-time development of our machines and technologies.
If you’re familiar with Loupe, you know that we’re all about revolutionizing our industry — and that means taking all the “what ifs” and turning them into action. We accomplish this through a process called New Machine Concept — our way of translating back-of-the-napkin ideas into workable blueprints.
For this inaugural season of Live at Loupe, we follow the team as they work through a real-life New Machine Concept — to create what we have lovingly dubbed the “Trak Packer.”
Inspiration
At 2018’s International Manufacturing Technology Show (IMTS), our partners at B&R unveiled a revolutionary new technology called ACOPOStrak — a flexible transport system that extends the economy of mass production down to batches of one. Our founders, David Nichols and Karl Robrock, saw this technology firsthand in Austria and began to ruminate on all the exciting machine possibilities it introduced.
One possibility that intrigued us was packaging — and in particular, the ability to case pack a wide variety of product inputs without any changes in hard tooling. As those of you in automation know, changeover is often a huge time suck in packing; you can lose 30–60 minutes each time you transition to a new product or case type.
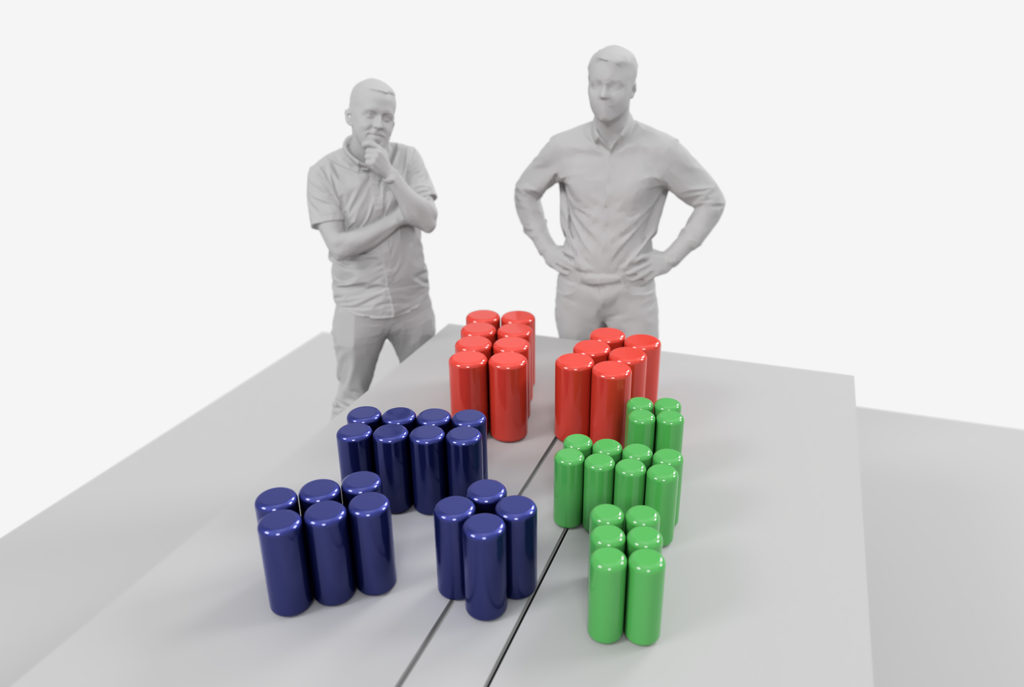
And so, the fundamental question guiding our discovery became:
“What if there was a machine that could transition between different product configurations without any changes in hard tooling?”
Discovery
This concept would use a unique end effector in cooperation with the new ACOPOStrak technology to eliminate the need to retool and cut the downtime dramatically.
This was the seed that would eventually grow into a fully-fledged New Machine Concept — the back-of-the-napkin idea that we used as our jumping off point. But first, we needed to get the rest of the team onboard — and discuss what would need to happen to turn this idea into reality. In New Machine Concept, that means assembling the concept team to present the sketch.
You can experience this initial discussion in the pilot episode of Live at Loupe — where we invite ACOPOStrak expert Derrick Stacey from B&R to join our NMC team to get clear about just what we’re trying to accomplish here and why.
At Loupe, one of our core values is “Trust in Collaboration” — and our team doesn’t disappoint. True to form, in this part of the process we address all the necessary considerations that could impact viability. Our team brings hard questions like, “What happens when you whip the product around a corner? What kind of speeds and accelerations and throughput do we need it to handle? Is it possible to measure the acceleration force of the shuttle?”
We have our work cut out for us.
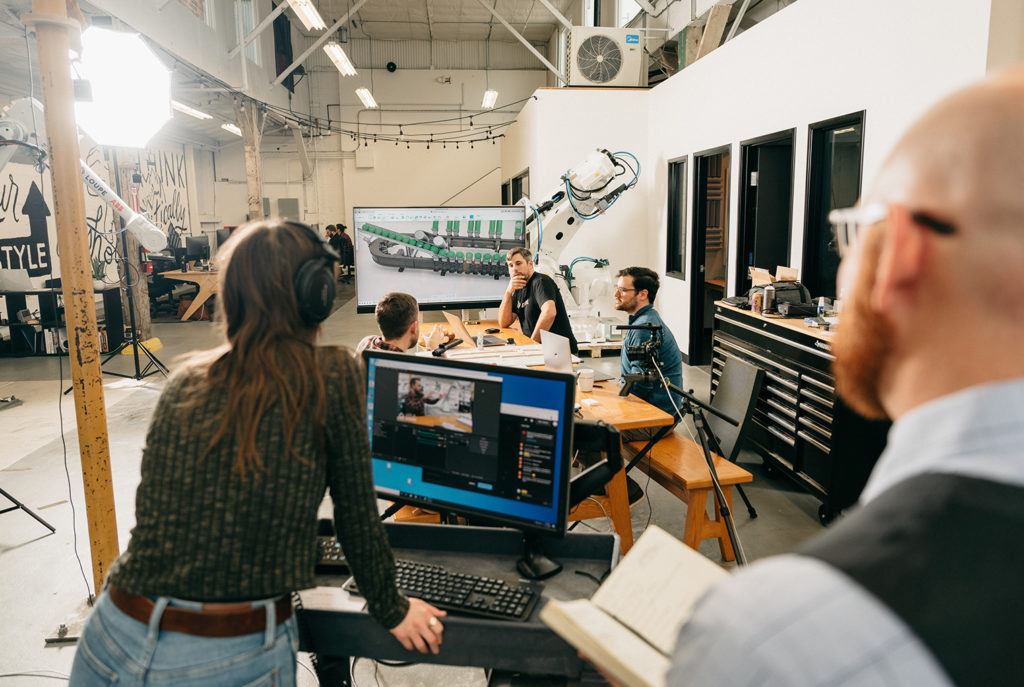
Refinement
As you may expect, this stage requires a lot of flexibility as we learn more about how to make this machine possible. Getting into the weeds is a natural part of the process. Our team sets to work answering the questions that came up in our discovery meeting — and you can see some of these answers in Episode 2 of Live at Loupe.
One such question is how to handle the infeed mechanisms to eliminate (or reduce) unconstrained movement of an object when it enters a shuttle. To do this, we fix the belt parallel to the opposite surface — forcing the object to straighten itself out.
Another challenge we face is timing. We work on tuning the balance between infeed speed, number of shuttles, and track length to hit the highest case output while leaving some wiggle room for process delays or other interruptions.
We bring the results from our timing studies to Episode 3, where we unlock some interesting possibilities — including revisiting the layout into a rectangular pattern. This allows us to bring the conveyor further downstream, providing more buffer and allowing a divert loop to be positioned at either end. This makes the track section shorter while still achieving the same throughput.
We also take a tour of the design in CAD and outline the controls architecture that will make it all possible — including how to control the B&R and ABB systems together.
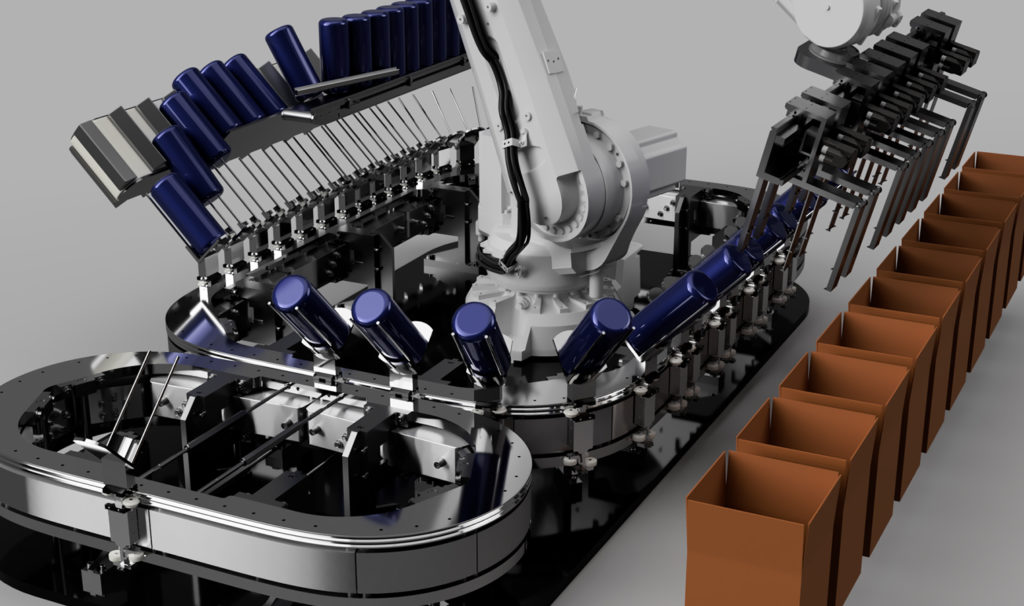
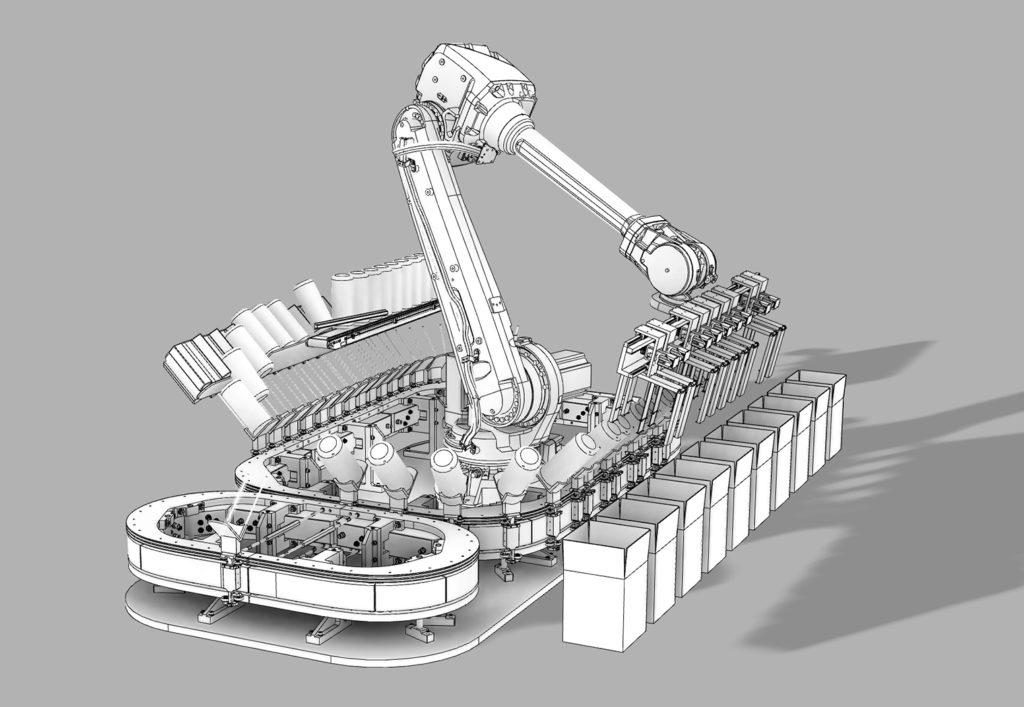
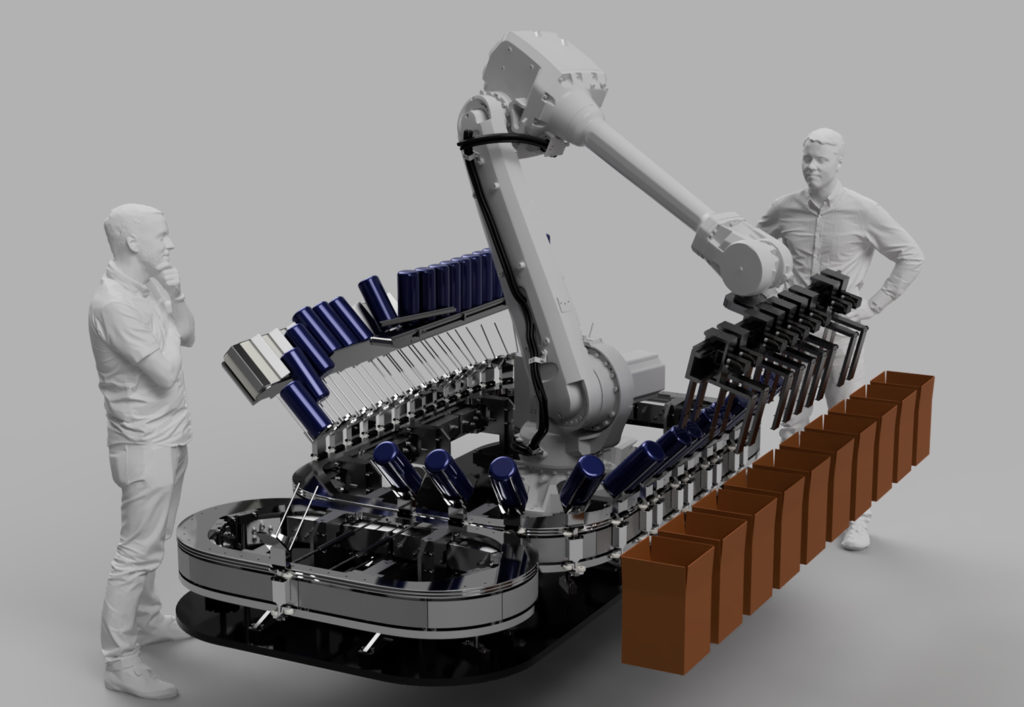
Pitch
As a final step of our New Machine Concept, we get ready to pitch our completed idea to the client. We do this together in our Season 1 finale of Live at Loupe. For this stage, our goals are to present our findings for the “machine of the future” we investigated, share a parts list for what it would take to build, and review the overall architecture that make it possible.
Our goal at this point is to build the pitch presentation together. This includes a discussion of what we’re explaining and how to make it as easy to understand as possible — as well as how to demonstrate the value of investment in certain critical components to:
- Change product types in seconds with dynamic staging
- Use the same tooling for all products
- Meet throughput targets
- Recover more gracefully from rejects or mis-picks
- Free up space for the end user
In addition, we start thinking through what development could look like — and how we could prototype this New Machine Concept in a six-week sprint. (Learn more about our Ship in Six philosophy here.)
Interested in seeing the final product? In a matter of weeks, we bring the Trak Packer from a back-of-the-napkin sketch to a viable machine concept. Hear our CEO, David Nichols, as he shares the outcome of this work – and the next steps to bring this solution to market.
Through the course of this process, we determine the correct track layout, explore iterative CAD designs, and review the timing studies and controls architecture of our revolutionary New Machine Concept. This stage not only clarifies objectives and expectations, but allows us to workshop potential risks and solutions. This is the magic of Loupe’s revolutionary approach to product development.
Or, to quote our CEO and Co-Founder David Nichols:
“We don’t just show up with this amazing concept. It takes a lot of hard work, creativity, collaboration, and arguing. That’s what we’re excited about doing. That’s why we come to work every day.”
Thanks again for joining us for our first season of Live at Loupe! Stay tuned for more next season, as we explore the real-time development of more revolutionary machine concepts and technologies.