Collaborations
Integrated Automation and Robotics from B&R and ABB
There are a number of interesting ways to connect B&R controls with ABB Robotics, and opportunities made possible by their compatibility.
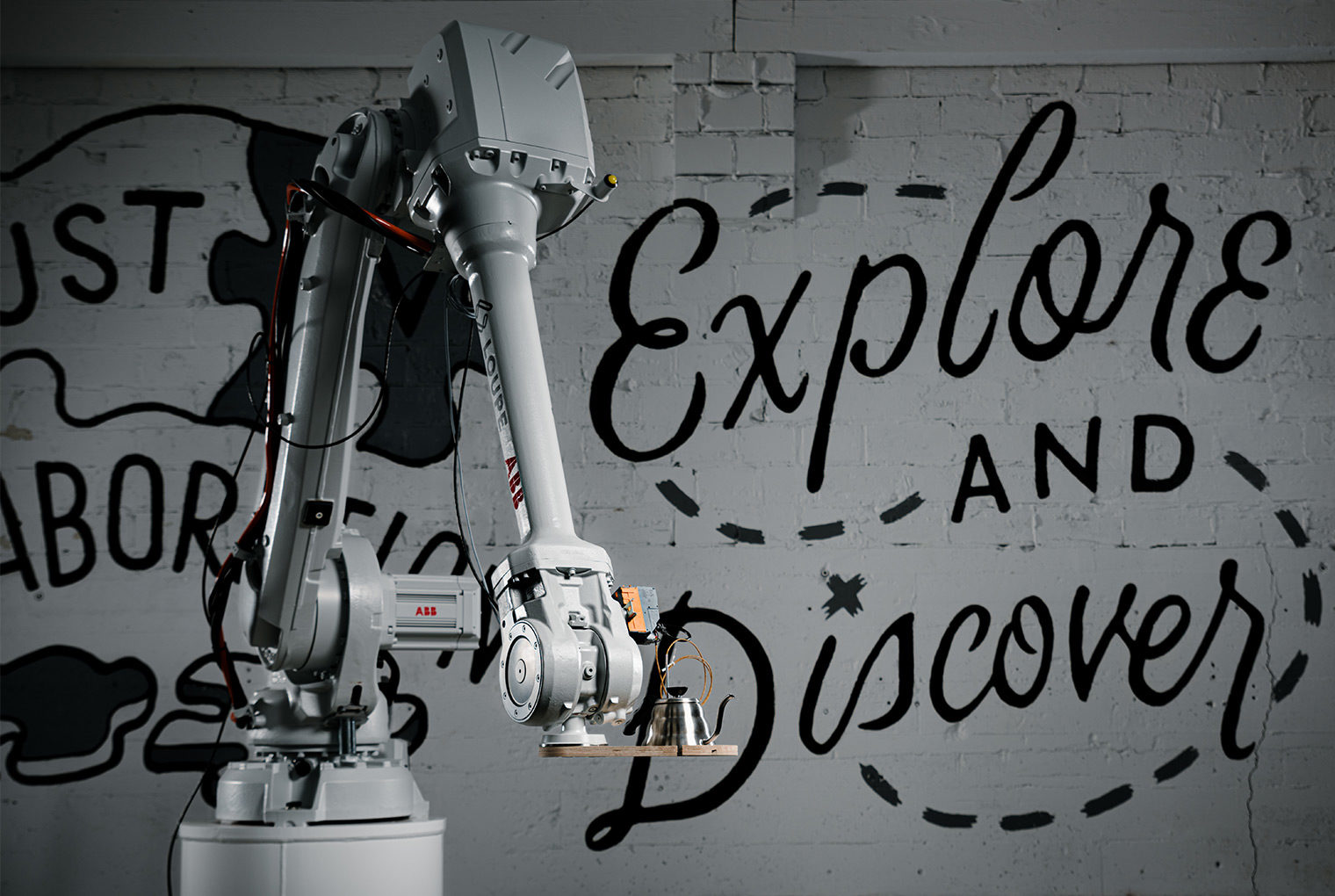
In our line of work, the terms “automation and robotics” are often lumped together. But technically, “robotics” refers only to the robot arm while “automation” is everything around it. Robots in production cells are nearly always surrounded by additional user interfaces, PLCs, servo motion, and safety.
Unfortunately, robots and their automation are often two giant (and separate) stacks of technology that come from different companies and don’t connect well.
But what if that didn’t have to be the case?
Since the acquisition of B&R Industrial Automation by ABB in 2017 and internal moves in the meantime, both of these technologies share a single division within ABB. So they have a strategic interest in these products complementing each other — and they’ve made strong investments with that in mind. As a result, there are a number of interesting ways to connect B&R controls with ABB Robotics, and opportunities made possible by their compatibility. We’ll cover a few here.
The Benefits of Connecting B&R and ABB
It’s a no-brainer that working with one company rather than two creates efficiencies by eliminating the need to coordinate communication between systems. But the unification of these platforms goes even further than convenience, by making machines more capable. Merging robotics with machine control into one unified architecture offers unprecedented levels of machine flexibility, precision, and synchronization:
- Enjoy a fully integrated automation system
- Shrink machine footprint with only one controller and engineering system
- Improve precision to the microsecond range
- Reduce development times with only one application and one development environment
- Lower the barrier to entry with a digital twin
- Achieve faster commissioning and engineering
The Future of Robotics & Automation
This integrated approach not only creates a seamless experience for users, it also introduces new, never-before-conceived machine possibilities. Here are two we’re excited about:
Machine Centric Robotics
Machine Centric Robotics represents the “Holy Grail” of robotic integration. This moves all the functionality of the robotics controller into the heart of the machine control system. To learn more about Machine Centric Robotics, check out this video from B&R which provides a high-level overview of how it works.
But its benefits extend far beyond that of a single software platform. If you’re familiar with Loupe, you know we’ve long understood the advantages of unified robots and controls — and in fact, have spent years doubling down on these revolutionary integrations. Our approach to Machine Centric Robotics takes these possibilities to a whole new level.
ABB and B&R are rolling out MCR versions of most ABB robots over the next 1–2 years. This option creates a perfectly orchestrated solution that can be scaled and rearranged with minimal effort to handle new products and dynamic batch sizes.
OPC UA and TSN
OPC UA and TSN promise to change the face of industrial data collection and processing.
Open Platform Connectivity and Unified Architecture (OPC UA) is the next generation of OPC — a more flexible and secure way to handle the volume and complexity of today’s data world. Time-Sensitive Networking (TSN) is a set of standards that provides deterministic networking for OPC UA.
Nowadays, the world of industrial automation faces new concepts — such as data analytics, cloud access, and edge computing. Data originating on devices may need to be preprocessed, filtered, and communicated to the cloud for management presentation and analytics. Currently, this data is often retrieved by fieldbus technologies — and to access it, you need gateways specific to the particular fieldbus.
However, OPC UA can unify the information models for all system devices to provide enhanced and transparent data access, using TSN as transport means. This also allows for the unification of the software, interfaces, and access models across product ranges.
The combination of these two technologies can provide two features vital for the future of industrial automation: a fast and robust data transport, and a client-server combination for elaborate device semantics.
Learn more about these emerging technologies and the machine possibilities they introduce in this article from ABB or via the technical reference manual.
A Spectrum of Interface Options
Aside from the machine potential these two opportunities present, there are a number of additional networks to connect these two products that each bring interesting new performance attributes.
Unified Safety via ProfiSafe
With ProfiSafe added to an ABB robot and to the supporting B&R control system, two safety systems become one.
All new kinds of collaborative concepts can be brought to production when robotic and conventional safety systems can coordinate in such a fast and articulate way, and when wrapped in the appropriate safety monitoring equipment and intelligent safe reaction behaviors.
(Interested in digging deeper? Learn how to configure ProfiSafe communication between a B&R safe PLC and an ABB robot controller.)
Fast Streaming Joint and TCP Control via Externally Guided Motion (EGM)
EGM is a way to take complete control of the robot pose (TCP, Joint, or offset from path) via outside systems as well as allow the robot to communicate its current position. It transports this data via UDP and Protocol Buffers with four-millisecond update times. Synchronizing the robot path to standard PLC and motion control systems enables many new processes that are time- and position-dependent.
For applications with complex dispensing, real-time control via sensor and vision systems, or highly responsive user interfaces, EGM can be a great interface choice.
To learn more, check out one example of a C++ library for interfacing from ROS to ABB robot controllers supporting EGM, as well as a conceptual sketch of how EGM works.
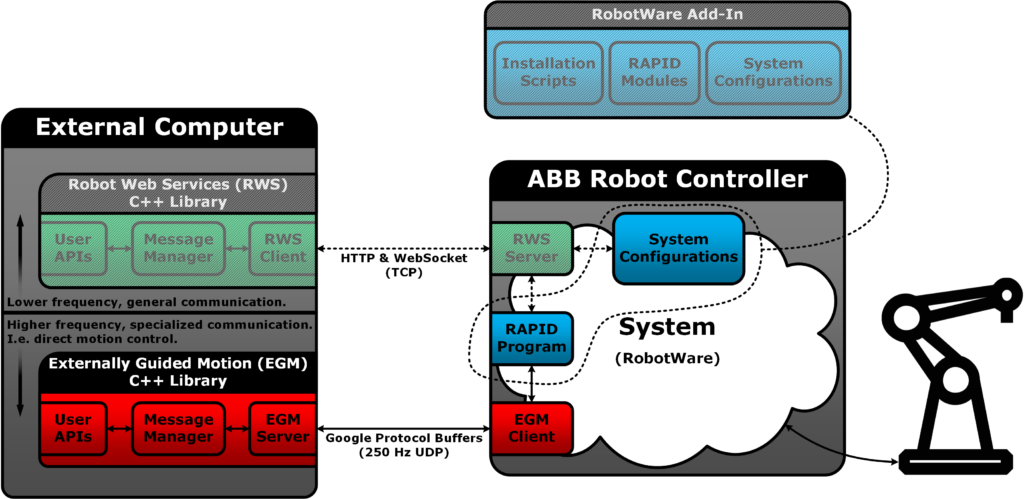
Robot Web Services and Loupe’s a3br Library
Loupe’s a3br (ABB+B&R) library provides programmatic access to an ABB robot from a B&R PLC via ABB’s Robot Web Services interface. This interface allows the caller to authenticate with the robot system and perform a variety of system functions. Currently supported functions include high-level execution commands (starting/stopping a program, resetting, powering the motors), commands to retrieve the current state of the robot, and commands to read or write IO channels on the robot (both cyclically and acyclically). Planned expansions of the library will also cover loading-specific programs for execution, downloading external programs to the robot, requesting mastership, querying detailed robot error information, and jogging the robot. Additionally, the library is set up to facilitate user extensions should other RWS functions be needed.
Unlocking Machine Potential
At Loupe, we’re proud to partner with ABB and B&R as industry-leading providers of this revolutionary technology, because we believe powerful ideas shouldn’t be limited by hardware constraints. And with such a technical product, having one supplier vs. two means that one company both provides the product and also supports it.
With those logistical considerations out of the way, we can focus on the work that gets us up in the morning: imagining the future of machines. Loupe then uplevels these machine capabilities by curating a versatile portfolio of software — combining out-of-the-box, open-source, and custom Loupe code. As both a robotics supplier and a PLC / motion / interface supplier, Loupe’s engineers are well-versed in the intricacies of both ABB and B&R. Interested in learning more about how a unified architecture could take your machines to the next level? Let’s collaborate on a New Machine Concept today.