Precision Packaging on a Budget
We partnered with a leading packaging machinery company to streamline motion systems, reducing costs by 40% while maintaining precision and reliability.
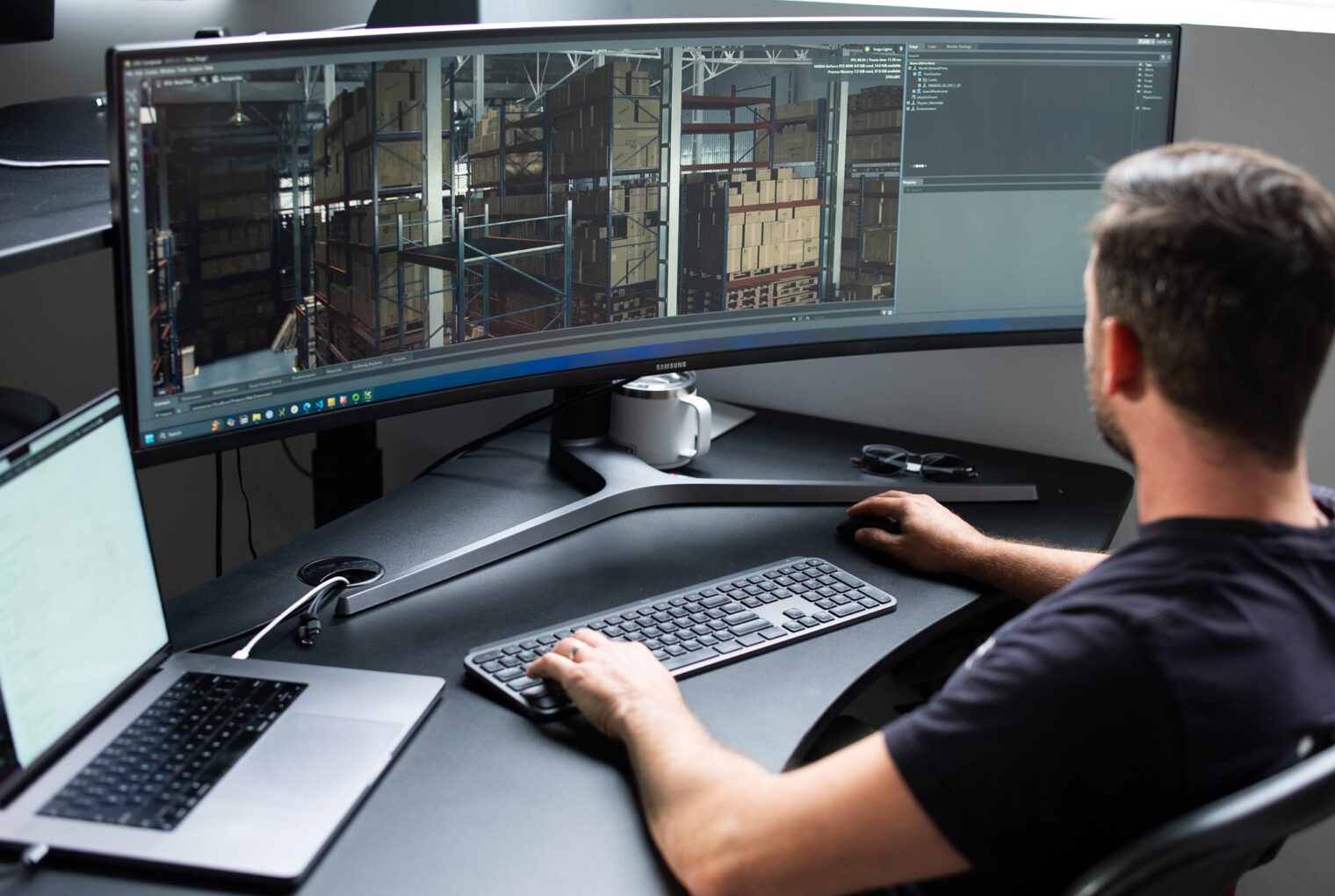
Our client is a leading company in the packaging machinery industry, renowned for producing both standard and robot-operated palletizers. They sought to enhance the efficiency and precision of their Rockwell-based motion systems — and faced with unique system constraints and cost pressures, they turned to Loupe.
THE NEED
Balancing Cost and Performance
The client’s motion system presented several technical constraints. At the core of the issue was the need to balance cost efficiency with reliable performance in a competitive, margin-sensitive industry.
- Hardware Footprint: The existing Rockwell-based setup required multiple components per motor, which increased cabinet size and complicated wiring configurations.
- Encoder Limitations: To maintain affordability, the system relied on 24 PPR encoders — a lower-performance option which presented challenges in maintaining the required precision.
- Cost Constraints: The client needed a solution that aligned with the tight margins typical of packaging machinery, while minimizing operational complexity.
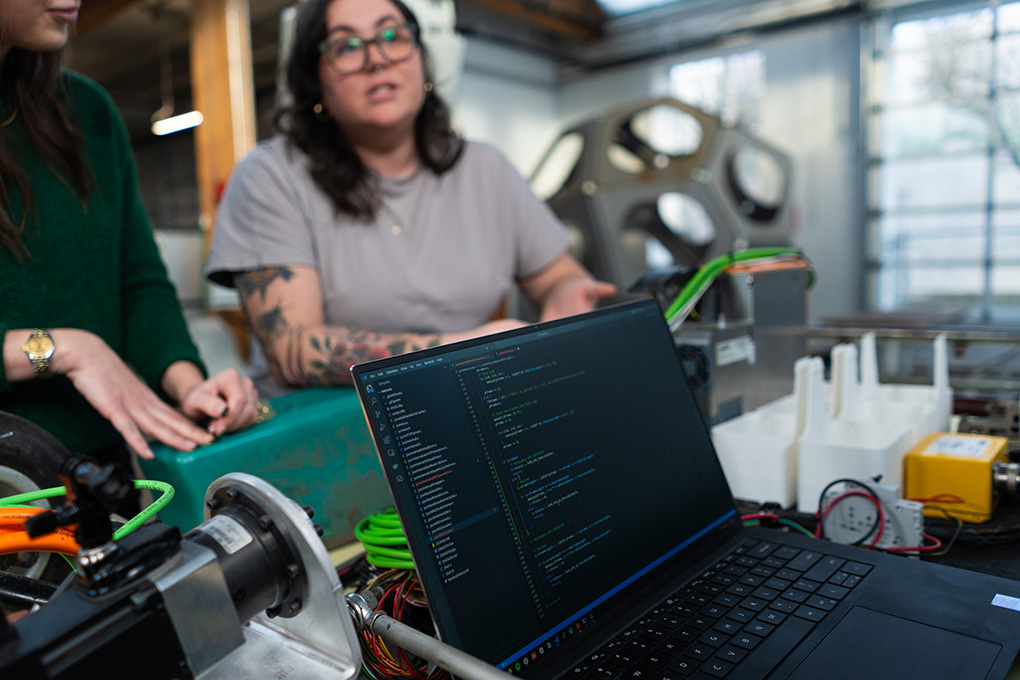
THE SOLUTION
Tailored Engineering for Low-Cost Constraints
Loupe designed and implemented a custom system that streamlined hardware, reduced complexity, and adapted to the constraints of low-cost components without compromise.
We did this by developing a custom rack-based system — reducing both number of devices and wiring complexity. To address the challenges posed by low-cost 24 PPR encoders, we employed speed adjustment strategies — using signals and precise adjustments to ensure placement accuracy. In this way, by utilizing asynchronous motors and other cost-effective components, we were able to deliver a solution that met budgetary requirements while maintaining operational reliability.
“Each device had to be programmed individually. With the new system, everything was uploaded automatically. If you wanted to change on a per-machine or per-motor basis, it was one point of contact. That’s huge.”
David Blackburn
Director of Engineering, Loupe
THE RESULT
Delivering Precision and Efficiency at Scale
Loupe’s work yielded measurable improvements that enhanced both the machinery and its operational efficiency:
- Reduced Footprint and Costs: The cabinet size and wiring requirements were reduced by approximately 40%, resulting in more efficient power usage and fewer devices to manage.
- Streamlined Configuration: A centralized configuration system eliminated the need for multiple individual connections, significantly simplifying installation and reducing ongoing maintenance needs.
- Client Impact: The packaging machinery became more efficient and reliable, supporting the client’s goals to balance complexity, cost efficiency, and precision.
Through innovative engineering and a commitment to cost-conscious solutions, Loupe delivered a tailored system that empowered this packaging machinery manufacturer to enhance their operations and achieve their strategic objectives… without compromise.