Revolutionizing Renewable Energy with Airborne Wind Turbines
The Makani airborne wind turbine pushed the limits of renewable energy — and ground operations. Discover how Ship in Six engineered an advanced ground station with precision winch control and synchronized motion systems, ensuring stability and success in extreme environments.
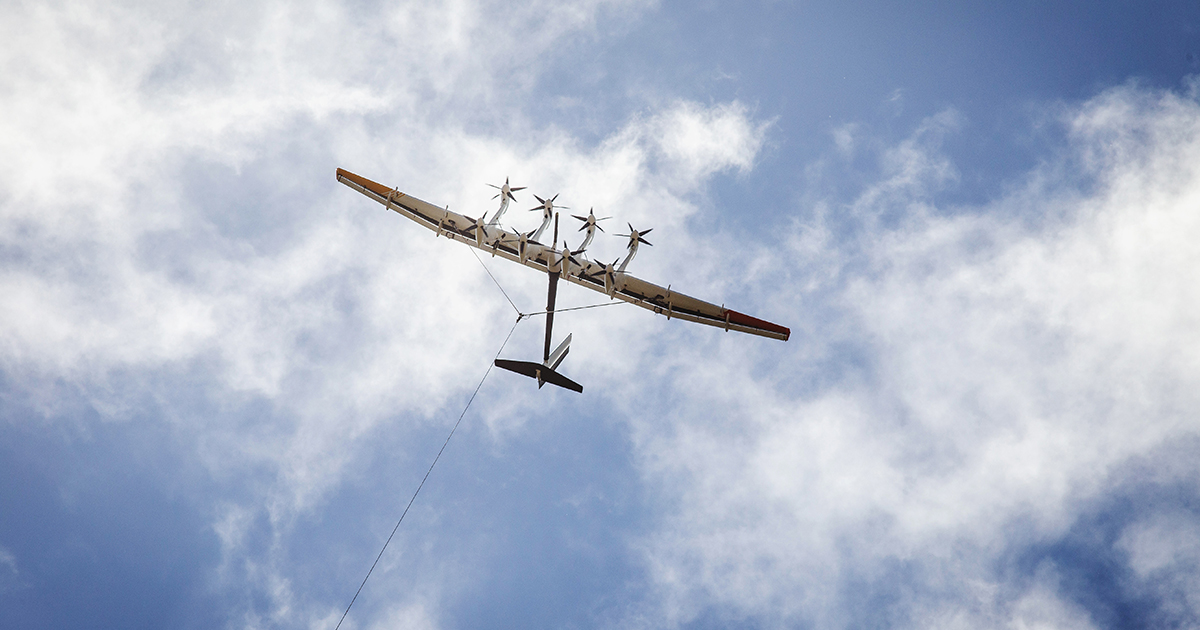
Makani, a pioneering renewable energy company, sought to push the boundaries of wind power generation. Their innovative concept centered around a “kite,” an airborne wind turbine designed to harness high-altitude winds more effectively than traditional wind turbines. This groundbreaking project required equally innovative solutions, particularly for the kite’s ground station — a critical component responsible for managing the tether and maintaining operational stability during flight.
THE CHALLENGE
Managing High-Tension Ground Operations
The Makani kite operated like a plane, ascending using onboard motors before diving to generate power. At the heart of the system was the ground station, tasked with controlling the kite’s tether under immense tension while synchronizing with flight control systems. The project presented several unique challenges:
- High-Performance Control: The ground station required an advanced winch system to manage the kite’s tether with precision, ensuring stability during flight cycles.
- Safety and Stability: The system had to safely handle the immense forces generated by the kite, which boasted a 50-foot wingspan.
- Operational Synchronization: Seamless integration with Makani’s flight control systems demanded collaboration across engineering teams.
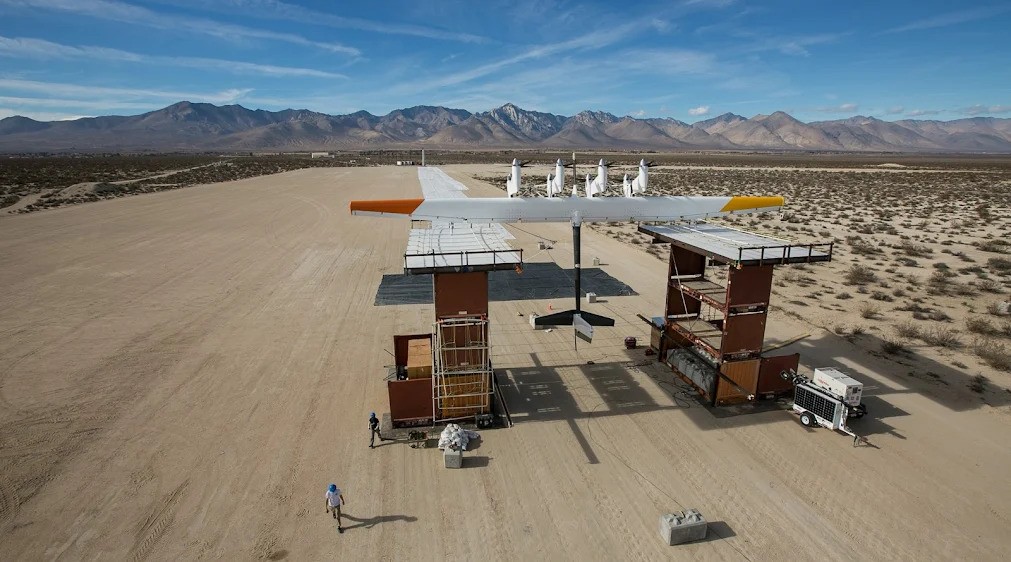
THE SOLUTION
Innovative Ground Station Engineering
Loupe’s expertise in high-performance control and motion synchronization was key to the project’s success. The team addressed Makani’s challenges through a combination of advanced engineering and collaborative development:
- Winch and Tether Management: Loupe developed a state-of-the-art winch control system featuring an auto-leveling capability to keep the tether stable and aligned throughout operation.
- Azimuth Control: By partnering with McLaren Applied Technologies, Loupe integrated precise control mechanisms for the kite’s Azimuth axis, ensuring smooth angle adjustments during ascent and descent.
- Turret Control System: Loupe introduced a novel turret control system that utilized multiple synchronized motors, later evolving into a standard offering for similar applications.
THE RESULT
Proven Technology for Renewable Energy Applications
Makani’s airborne wind turbine successfully demonstrated the potential of high-altitude wind power, thanks in part to Loupe’s innovative ground station solutions. Key achievements included:
- Successful Field Testing: The ground station supported test flights in the North Sea, delivering consistent reliability and precision even in challenging environments.
- Pioneering Motion Control: Loupe’s contributions showcased their leadership in synchronized motion control, earning recognition for advancing renewable energy technologies.
- Client Impact: Loupe played a vital role in Makani’s operational milestones, making automated, high-tension ground support a reality for airborne wind turbines.
“The Makani project stands as a testament to our ability to combine engineering expertise with innovative solutions, redefining what’s possible in renewable energy applications.”
— Josh Polansky, Technical Fellow, Ship in Six
Video provided by Makani